When choosing a CVD (Chemical Vapor Deposition) electric furnace for silicon dioxide coating, multiple key factors need to be considered to ensure that the equipment can meet the needs of experiments or production. Let’s take a detailed look at what aspects to pay attention to when choosing a CVD electric furnace for silicon dioxide film coating!
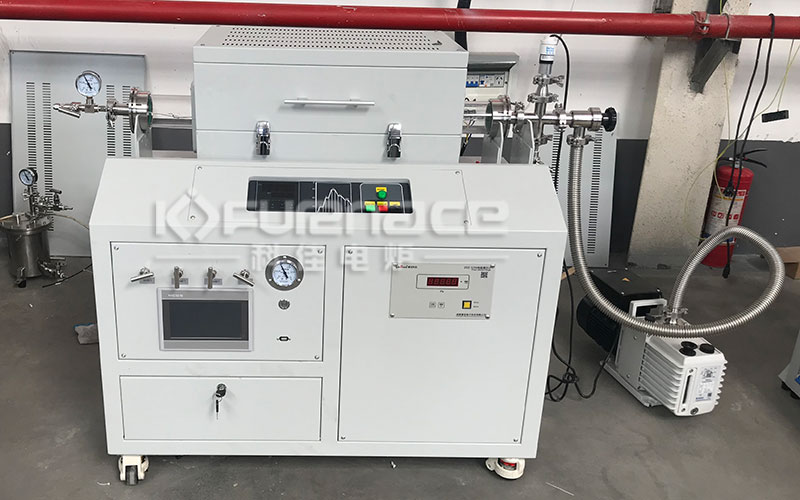
Commonly used CVD electric furnaces for silicon dioxide coating (click on the image to view product details)
1. Temperature range and stability
Temperature range: determined based on the maximum temperature and temperature stability required for coating. Ensure that the selected electric furnace can operate stably within the required temperature range. The common working temperature range for CVD tube furnaces is between 800 ℃ and 1700 ℃.
Temperature accuracy: High precision temperature control is important for the repeatability of coating quality. Choose an electric furnace with a high-precision temperature control system, such as equipment using PID automatic control, thyristor (thyristor) output power, 30 segment programmable controller, and other technologies.
2. Atmosphere control
Gas type: CVD process usually requires a specific atmosphere, such as inert gas, reducing gas, or oxidizing gas. For silicon dioxide coating, silicon source gas (such as silane) and oxidant (such as oxygen or nitrogen oxide) are usually required.
Gas flow control: Choose an electric furnace equipped with multiple flow meters (such as float flow meters and mass flow meters) to accurately control the intake air volume, ensuring the stability and controllability of the coating process.
3. Furnace and heating method
Furnace size: The furnace size should be large enough to accommodate the experimental sample and ensure that the sample can be uniformly heated during the heating process.
Heating method: The common heating method is resistance heating. Ensure the quality of the heating element is reliable, and the heating rate and temperature distribution meet the coating requirements.
4. Temperature uniformity
Heating zone and constant temperature zone: The heating zone determines the heating range inside the furnace tube, while the constant temperature zone determines the area of temperature uniformity. Choose an electric furnace with sufficient heating and constant temperature zones to ensure uniform heating of the experimental samples.
Temperature uniformity: The temperature of each part in the furnace should be as uniform as possible to avoid coating quality deviation caused by uneven heating of experimental samples.
5. Cooling system and safety performance
Cooling system: Cooling system is important for protecting equipment and ensuring experimental safety. Choose an electric furnace with a reliable cooling system to ensure stable operation of the equipment during the experiment.
Safety performance: Consider the safety performance of the electric furnace, such as overheat protection, leakage protection, emergency shutdown and other safety devices.
6. Equipment quality and after-sales service
Equipment quality: Choose well-known brands and manufacturers with good reputations to ensure the quality and reliability of the equipment.
After sales service: Understand the manufacturer’s after-sales service policy, including support for equipment installation and commissioning, technical training, maintenance, and other aspects.
7. User reviews and market feedback
User evaluation: Check the user’s evaluation of the selected device to understand the actual usage effect and existing problems of the device.
Market feedback: Understand the price, performance, and user feedback of similar devices in the market in order to make more informed decisions.
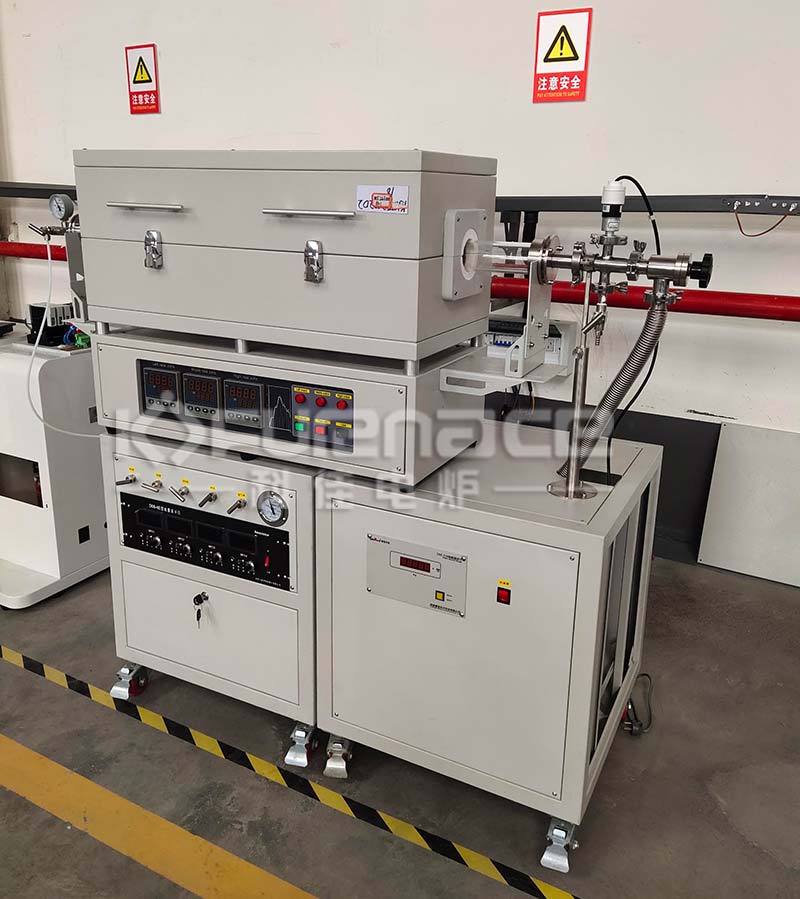
Multi temperature zone tubular CVD electric furnace (click on the image to view product details)
In general, when choosing a CVD electric furnace for silicon dioxide coating, it is necessary to comprehensively consider multiple factors such as temperature range and stability, atmosphere control, furnace and heating method, temperature uniformity, cooling system and safety performance, equipment quality and after-sales service, as well as user evaluation and market feedback. By comprehensively evaluating these factors, it can be ensured that the selected equipment can meet the coating requirements and provide strong support for your research or production work.Click to learn more CVD devices! Or click on online customer service to learn more about product information!