The application of vacuum sintering furnace in the field of ceramic sintering is very extensive, and its unique sintering environment and technological advantages provide strong support for the preparation of ceramic materials. Let’s take a closer look at the application of vacuum sintering furnaces in the ceramic industry!
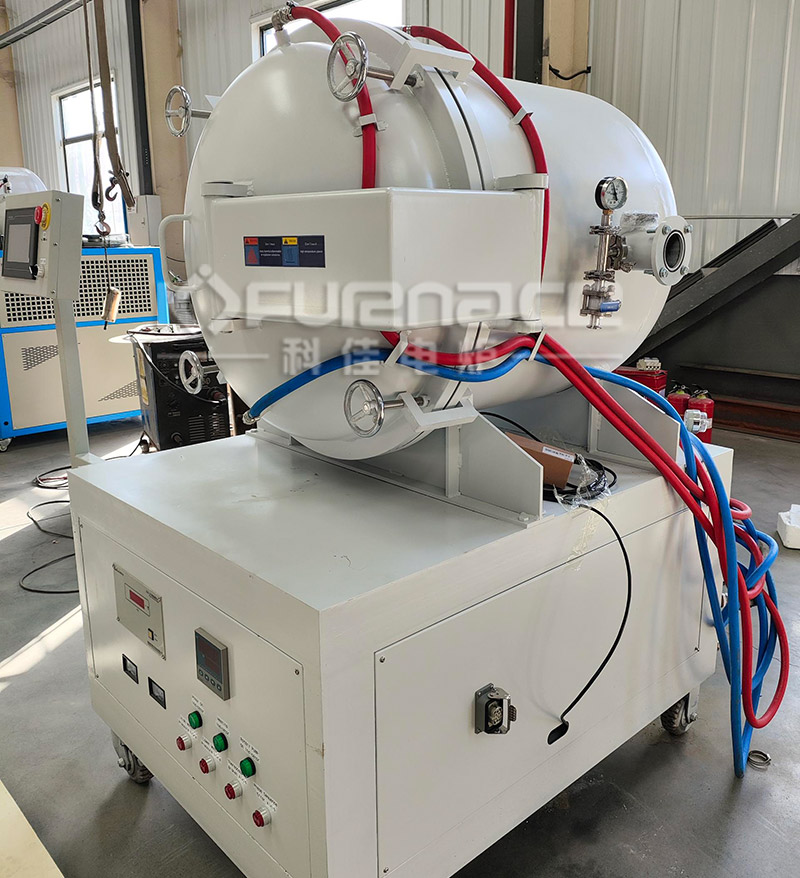
Commonly used vacuum sintering furnaces (click on the image to view product details)
1. Basic principles of vacuum sintering furnace
A vacuum sintering furnace is a device used for protective sintering of heated objects in a vacuum environment. It extracts air from the furnace through a vacuum system, creating a high vacuum environment, and then heats the materials inside the furnace through heating elements to achieve the desired sintering temperature. In a vacuum environment, the sintering process of materials is more uniform and stable, and can effectively avoid problems such as oxidation and pollution.
2. Application of Vacuum Sintering Furnace in Ceramic Sintering
Densification and performance optimization of ceramic materials:
During the preparation process of ceramic materials, vacuum sintering furnaces can achieve rapid sintering and densification of ceramic powders through high-temperature sintering, thereby improving the mechanical properties and thermal stability of ceramic materials.
The vacuum environment helps to reduce the oxidation and volatilization losses of ceramic materials during the sintering process, ensuring the quality and performance of sintered products.
Preparation of high-performance ceramic products:
By vacuum sintering treatment, high-strength and high hardness ceramic products can be prepared, which have broad application prospects in aerospace, electronic information and other fields.
Vacuum sintering furnace can also be used to prepare ceramic materials with special properties, such as superconducting ceramics, piezoelectric ceramics, etc.
Improve material purity and reduce pollution:
In a vacuum environment, ceramic materials do not undergo chemical reactions with oxygen or other gases, thus maintaining the purity of the material and avoiding the influence of impurities on its properties.
The vacuum sintering process reduces gas emissions and is beneficial for environmental protection.
3. Advantages of vacuum sintering furnace
Improving material properties: The vacuum environment facilitates atomic diffusion and rearrangement within the material, making it denser and more uniform, thereby enhancing its mechanical and thermal properties.
Expanding the scope of material preparation: Vacuum sintering furnaces are suitable for the preparation of various materials, including metals, ceramics, composite materials, etc., expanding the scope of material preparation.
Energy saving and emission reduction: Compared with traditional sintering processes, vacuum sintering furnaces have lower energy consumption during the sintering process, while reducing the emission of harmful gases, which meets the requirements of green and environmentally friendly production.
4. Application examples
In the aerospace field, vacuum sintering furnaces are used to prepare high-performance ceramic coatings and ceramic matrix composites to improve the high temperature resistance and corrosion resistance of aircraft.
In the field of electronic information, vacuum sintering furnaces are used to prepare high-performance electronic ceramic materials and magnetic materials to meet the demand of modern electronic industry for high-performance materials.
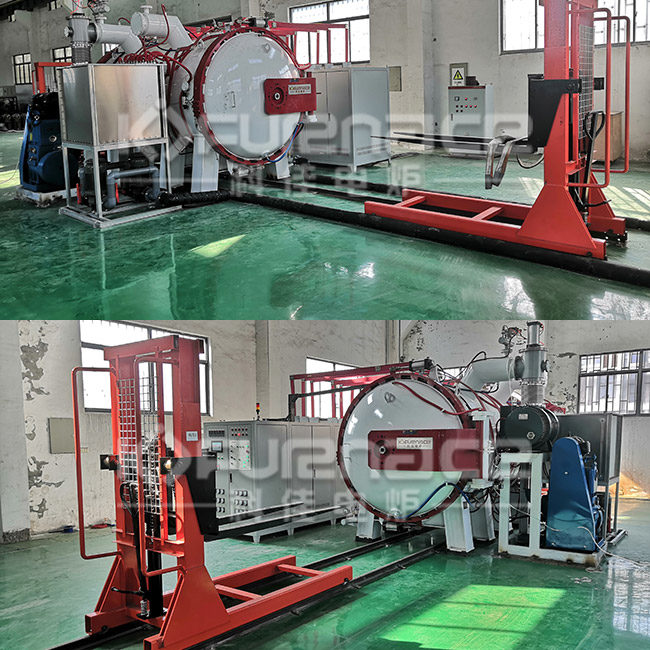
Industrial vacuum furnace (click on the image to view product details)
Overall, vacuum sintering furnaces have broad application prospects and many advantages in the field of ceramic sintering. With the continuous development of materials science and technological advancement, vacuum sintering furnaces will play an increasingly important role in the preparation of ceramic materials.Click to learn more vVacuum furnaces! Or click on online customer service to learn more about product information!