Under vacuum conditions, 1600 degree sintering is usually carried out using a vacuum sintering furnace, among which 1600 degree high-temperature vacuum tube sintering furnace and 1600 degree vacuum atmosphere protected sintering furnace are two common choices. Let’s take a detailed look at the characteristics of both types of stoves below!
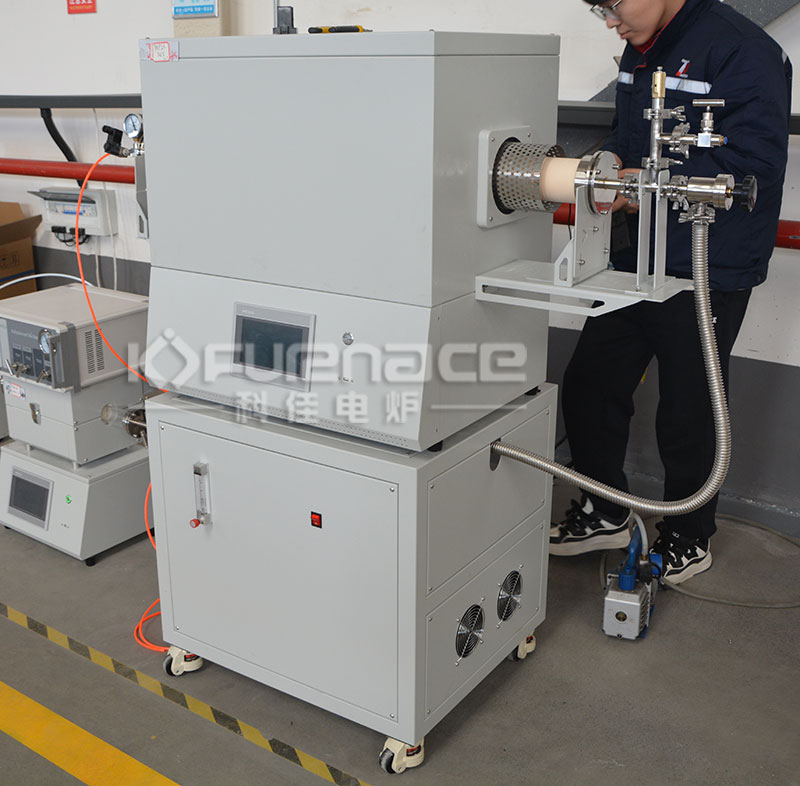
Commonly used high-temperature vacuum tube sintering furnace (click on the picture to view product details)
1600 ℃ high-temperature vacuum tube sintering furnace
This type of furnace is a common heat treatment equipment in the field of modern materials science. Its design allows researchers to achieve sintering processes in different temperature zones within the same furnace, greatly improving experimental efficiency. Meanwhile, a high temperature of 1600 degrees is an important condition for sintering many special materials. Its main advantages include:
Multi zone independent control: Different temperatures can be set and controlled in different areas to meet complex experimental requirements.
Atmosphere regulation: It can control and regulate the composition of the atmosphere inside the furnace, providing an ideal reaction environment for experiments.
Good temperature uniformity: By reasonable design and optimization, the temperature uniformity throughout the entire tube is ensured, ensuring the accuracy of experimental results.
Diversified sample processing: suitable for various sample forms and processing methods, such as powder, film, wire, etc.
Ultra high temperature capability: A high temperature of 1600 degrees can handle many high melting point and difficult to sinter materials.
Advantages of vacuum environment: Sintering under vacuum conditions can effectively eliminate the interference of gases and impurities, and improve the purity and performance of materials.
1600 ℃ vacuum atmosphere protection sintering furnace
This type of furnace also has the ability to operate in a vacuum or specific protective atmosphere (such as argon, nitrogen, etc.), which can greatly reduce the adverse effects of harmful components (water, oxygen, nitrogen, etc.) in the atmosphere on the product. This is crucial for sintering materials that are sensitive to the atmosphere, as it can effectively prevent phenomena such as material oxidation, decarburization, and carburization, ensuring the purity and performance of the product. Its main features include:
A good temperature control system: capable of achieving temperature regulation and stable temperature maintenance, with high temperature control accuracy.
Improving material properties: Vacuum can improve the wettability between liquid and solid phases, which is beneficial for material shrinkage and improvement of alloy structure.
Energy saving and efficient: reduces convection and thermal losses of gas, and the furnace material usually uses high-quality insulation materials with low heat loss and good insulation effect.
High process flexibility: Different parameters such as vacuum degree, atmosphere type, gas flow rate, and sintering temperature curve can be selected according to different materials and process requirements.
Safe and reliable: It has multiple safety protection designs, such as over temperature alarm, power outage protection, etc.

A commonly used 1600 degree graphite vacuum atmosphere protection sintering furnace (click on the picture to view product details)
Overall, both the 1600 degree high-temperature vacuum tube sintering furnace and the 1600 degree vacuum atmosphere protected sintering furnace are ideal choices for sintering at 1600 degrees under vacuum conditions. The specific choice of furnace depends on the specific requirements of the experiment and the characteristics of the material.Click to learn more furnace! Or click on online customer service to learn more about product information!