When choosing a high-temperature vacuum brazing furnace, multiple aspects need to be considered comprehensively to ensure that the selected equipment can meet production needs, improve welding quality, and ensure operational safety. Let’s take a detailed look at the specific precautions below!
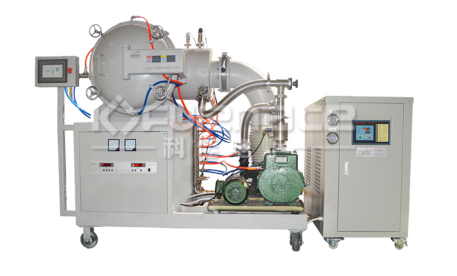
A commonly used high-temperature vacuum brazing furnace (click on the image to view product details)
1. Clear usage requirements
Workpiece size and load-bearing capacity
Workpiece size: Select a furnace with sufficient effective working area based on the maximum size and shape of the workpiece to be welded. The effective workspace should be able to accommodate workpieces and leave appropriate operating space.
Load bearing capacity: Ensure that the load-bearing capacity of the furnace is greater than the weight of the workpiece, including the weight of fixtures and trays.
Temperature requirements
Maximum working temperature: Select a furnace with sufficient maximum working temperature based on the melting point and process requirements of the brazing material.
Temperature uniformity: Pay attention to the temperature uniformity inside the furnace to ensure the consistency of welding quality. Temperature uniformity is usually evaluated through multi-point temperature measurement.
Vacuum requirement
Ultimate vacuum degree: Select a furnace with an appropriate ultimate vacuum degree according to the requirements of the brazing process. High vacuum degree helps reduce oxidation and pollution during the welding process.
Working vacuum degree: Understand the ability of the furnace to maintain vacuum degree during operation.
2. Furnace performance and configuration
Heating system
Heating element: Choose heating elements that are resistant to high temperatures and corrosion, such as molybdenum screens or graphite heaters.
Heating method: Consider the layout of heating elements and heating method to ensure temperature uniformity.
Temperature control system: Choose a high-precision temperature control system, such as a programmable temperature controller, to achieve precise temperature control.
vacuum system
Vacuum pump group: Understand the configuration of vacuum pump groups, including mechanical pumps, Roots pumps, and diffusion pumps, to ensure that the required vacuum degree can be met.
Vacuum testing: Ensure that the furnace is equipped with vacuum gauges and other testing equipment to monitor the vacuum level in real time.
Cooling system
Cooling method: Understand the cooling methods of the furnace, such as gas cooling, water cooling, etc., to ensure that the workpiece can cool quickly after welding is completed.
Cooling effect: Pay attention to the effectiveness of the cooling system to avoid deformation or cracking of the workpiece due to uneven cooling.
safety performance
Interlocking protection: Choose furnaces with interlocking protection functions, such as over temperature power-off, over pressure alarm, water cut-off delay shutdown, etc., to ensure operational safety.
Emergency shutdown: Ensure that the furnace is equipped with an emergency shutdown device to quickly shut down in case of abnormal situations.
3. Operation and maintenance
Ease of operation
Automation level: Consider the automation level of the furnace, such as whether it has automatic temperature control, automatic inflation and deflation functions, to improve operational efficiency.
Human machine interface: Choose a furnace with a user-friendly interface, such as a touch screen control system, so that operators can easily set and monitor parameters.
Maintenance
Replacement of vulnerable parts: Understand the replacement cycle and methods of vulnerable parts in the furnace, in order to carry out timely maintenance and upkeep.
After sales service: Choose a supplier that provides good after-sales service so that you can receive timely technical support and maintenance services during use.
4. Cost considerations
equipment price
Cost effectiveness: Choose a furnace with high cost-effectiveness based on budget and requirements. Do not blindly pursue high or low prices, but focus on the performance and configuration of the furnace.
operating cost
Energy consumption: Considering the energy consumption of the furnace, choose energy-saving furnaces to reduce operating costs.
Consumable cost: Understand the cost of consumables (such as vacuum pump oil, protective gas, etc.) that need to be consumed during the use of the furnace.
5. Brand and reputation
Brand awareness
Industry reputation: Choose brands with good industry reputation and visibility to ensure the quality and reliability of equipment.
User Evaluate
Case reference: Understand the usage of the furnace in other users, including welding quality, equipment stability, after-sales service, and other aspects.
6. Other precautions
environmental requirements
Emission standards: Ensure that the furnace meets local environmental requirements, such as exhaust emission standards.
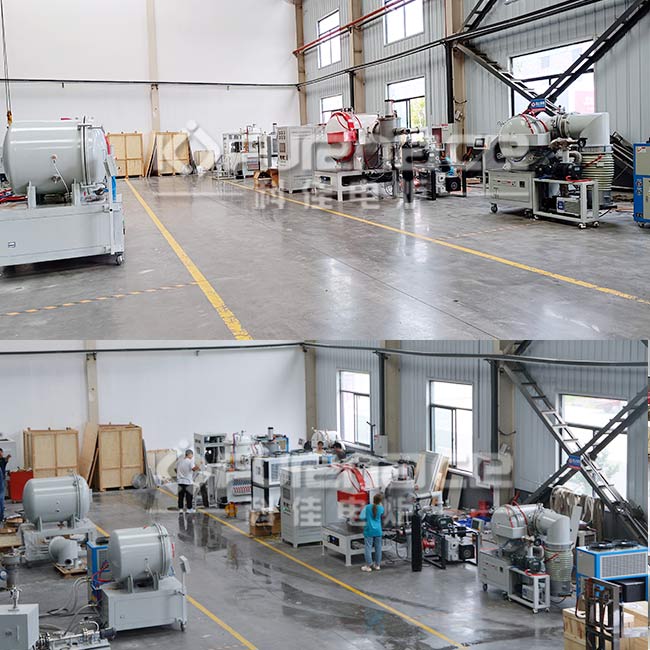
Regular maintenance of the vacuum furnace is also an important means to reduce malfunctions
Installation and debugging
Installation requirements: Understand the installation requirements of the furnace, including requirements for power, water, and gas sources.
Debugging and acceptance: Select suppliers who provide installation and debugging services, and conduct strict acceptance and debugging after the equipment arrives.Click to learn more Vacuum Furnaces! Or click on online customer service to learn more about product information!