When choosing a vacuum powder hot pressing sintering furnace, multiple factors need to be considered comprehensively to ensure that the equipment can meet the production process requirements, improve product quality and production efficiency. Common hot press sintering furnaces generally include tubular hot press sintering furnaces and vacuum hot press sintering furnaces. Let’s take a detailed look at how to choose!
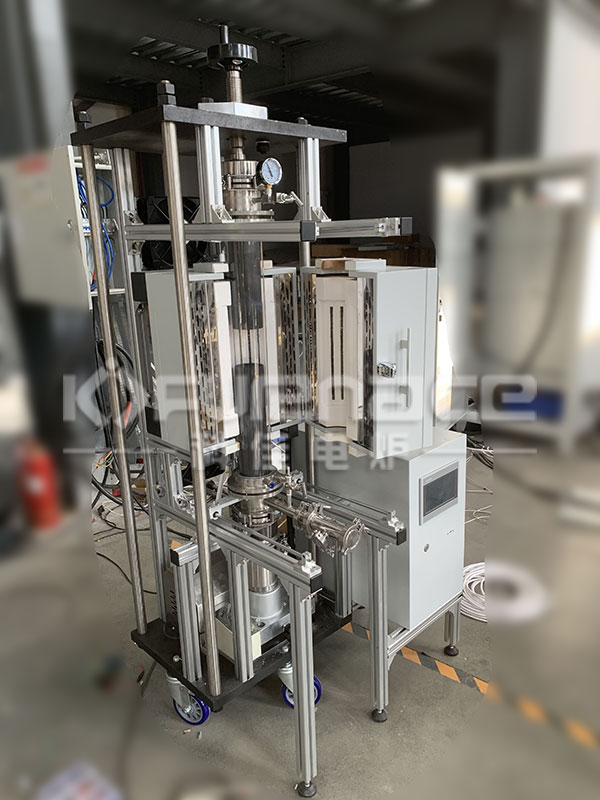
Graphite tube hot press furnace
1. Clarify process requirements
Temperature range: Determine the maximum sintering temperature required based on the characteristics of the sintered material and process requirements. For example, certain ceramic materials may require sintering temperatures of up to 2000 ℃ or higher.
Vacuum degree requirements: Different processes have different requirements for vacuum degree, ranging from low vacuum to high vacuum or even ultra-high vacuum. High vacuum helps reduce material oxidation and improve sintering quality.
Pressure requirement: Hot pressing sintering requires applying a certain amount of pressure to promote the bonding between powder particles. Select the appropriate pressure range and pressurization method based on the material properties.
2. Consider product specifications and production capacity
Furnace size: Select the appropriate furnace size and volume based on the product size and batch size. Ensure that the furnace can accommodate the workpieces to be sintered and leave appropriate space for easy access.
Production efficiency: Consider the heating rate, cooling rate, and degree of automation of the equipment to improve production efficiency and reduce labor intensity.
3. Pay attention to equipment quality and stability
Heating element: Choose heating elements with high thermal conductivity, low deformation at high temperatures, and low heat loss, such as tungsten molybdenum wire, graphite, etc. Ensure that the material of the heating element does not affect the quality of the workpiece.
Heat shield: The heat shield is the main component of the vacuum furnace heating chamber and has a significant impact on the power and performance of the equipment. Choose insulation screen materials that have good heat resistance and can effectively block heat convection, such as tungsten molybdenum materials.
Vacuum system: A good vacuum system can quickly achieve the required vacuum degree and maintain a stable vacuum environment. To understand the performance and configuration of vacuum pumps such as mechanical pumps and Roots pumps.
Control system: Choose a system with high-precision temperature control and pressure control to ensure the stability and repeatability of the sintering process. At the same time, consider the usability and maintainability of the system.
4. Pay attention to energy-saving performance and environmental protection requirements
Energy saving technology: Choose a vacuum sintering furnace that adopts energy-saving technology, such as optimizing the layout of heating elements, using high-efficiency insulation materials, etc., to reduce energy consumption and operating costs.
Environmental requirements: Ensure that the equipment complies with local environmental regulations and standards, and reduce the discharge of waste gas and wastewater. Consider the cooling method and medium of the equipment, and choose an environmentally friendly and economical cooling solution.
5. Consider price and after-sales service
Equipment price: Choose the appropriate equipment model and configuration based on budget and actual needs. When comparing prices, factors such as equipment performance, quality, and after-sales service should be comprehensively considered.
After sales service: Choose a supplier with a good after-sales service system to ensure that the equipment can receive timely technical support and maintenance services during use. Pay attention to the supply and replacement costs of vulnerable parts to reduce long-term operating costs.
6. Other precautions
Special gas compliance: If special gases (such as protective gases, reaction gases, etc.) need to be introduced during the sintering process, it is necessary to ensure that the equipment has corresponding gas introduction and control functions.
Uniformity of temperature zone inside the furnace: Test the temperature uniformity at different temperature points to ensure uniform temperature distribution inside the furnace and improve sintering quality.
Cooling speed: Consider whether the equipment has a rapid cooling function to meet the cooling needs of different materials.
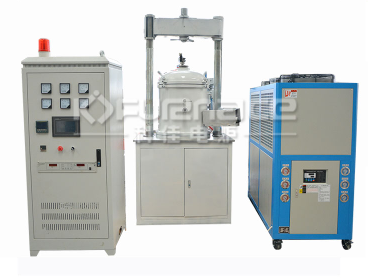
A vacuum hot press furnace with higher vacuum degree (click on the picture to view product details)
In general, when choosing a vacuum powder hot pressing sintering furnace, it is necessary to comprehensively consider multiple factors such as process requirements, product specifications, equipment quality, energy-saving performance, price, and after-sales service. It is recommended to communicate with professional equipment suppliers and customize suitable equipment solutions based on actual needs.Click to learn more Heat treatment equipments! Or click on online customer service to learn more about product information!