When choosing a vacuum furnace for silicon carbide sintering, multiple aspects should be considered comprehensively to ensure that the selected equipment meets production needs, improves product quality and production efficiency. Let’s take a detailed look at what to pay attention to when choosing a vacuum silicon carbide sintering furnace!
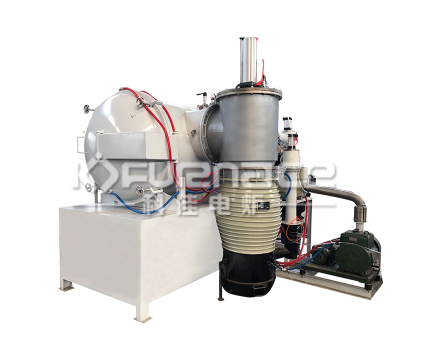
1500 ℃ vacuum sintering furnace (click on the picture to view product details)
1. Clearly define production needs and objectives
Material type and batch size:
Consider the type, shape, and size of silicon carbide material that needs to be sintered.
Determine the size of the production batch in order to choose the appropriate furnace size and heating power.
Sintering temperature and atmosphere:
Clearly define the maximum temperature and temperature uniformity requirements for sintering.
Determine whether a specific sintering atmosphere (such as inert gas) is required.
Equipment budget and frequency of use:
Set a reasonable equipment budget based on the economic situation and investment plan of the enterprise.
Consider the frequency of device usage and choose devices with good durability and stability.
2. Pay attention to the technical parameters of the equipment
Furnace size and volume:
Choose a furnace size that is large enough to accommodate the required silicon carbide workpieces.
Consider effective capacity to ensure it can meet the needs of large-scale production.
Heating power and temperature range:
Ensure that the heating power is sufficient to quickly raise the temperature to the desired sintering temperature.
Choose equipment with a wide temperature range to adapt to different sintering processes.
Vacuum degree and sealing performance:
Choose equipment with high vacuum degree to ensure the quality and performance of sintered materials.
Pay attention to the sealing performance of the equipment to prevent external gases from entering the furnace and contaminating the sintered materials.
Temperature control accuracy and uniformity:
Choose equipment with high temperature control accuracy to ensure the accuracy of sintering temperature.
Pay attention to the uniformity of temperature inside the furnace to avoid quality problems caused by local overheating or undercooling.
3. Consider the heating method and furnace type of the equipment
Heating method:
Electric sintering furnace: high energy utilization rate, good environmental performance, suitable for small batch and high-precision sintering requirements.
Furnace type selection:
Tube sintering furnace: suitable for sintering slender rod-shaped or tubular materials.
Bell type sintering furnace: suitable for large-scale and continuous production.
Vacuum sintering furnace: suitable for impurity free, high vacuum sintering of silicon carbide, with better cleanliness.
4. Evaluate the control system and automation level of the equipment
Control system:
Choosing equipment equipped with a good control system can achieve precise control and real-time monitoring of process parameters such as temperature and vacuum degree.
The control system should have data recording and traceability functions to analyze and optimize the production process.
Automation level:
Improving the automation level of equipment can reduce manual operation errors and enhance production efficiency.
Consider whether remote monitoring and intelligent control functions are needed to keep track of the device’s operating status at all times.
5. Pay attention to auxiliary devices and safety measures
Auxiliary device:
Based on actual needs, consider whether it is necessary to equip auxiliary devices such as atmosphere control devices and cooling systems.
These devices can further enhance the performance and adaptability of the equipment.
Safety measures:
Choose equipment with comprehensive safety protection functions, such as over temperature alarm, water cut-off protection, etc.
Ensure that the equipment complies with relevant safety standards and regulations to ensure the safety of operators.
6. Assess the professional level and after-sales service of the manufacturer
Professional level:
Choosing a manufacturer with rich experience and professional skills can ensure the quality and performance of the equipment.
Understand the manufacturer’s research and development capabilities and technological innovation capabilities in order to choose products with better technology.
after-sale service:
Choosing a manufacturer that provides excellent after-sales service can ensure the long-term stable operation of the equipment.
Consider whether it is necessary to provide value-added services such as technical training and equipment maintenance.
7. Reference market feedback and user evaluations
Market feedback:
Understand the usage and feedback of similar products in the market.
Pay attention to the dynamics and trends within the industry in order to select equipment that meets market demand.
User reviews:
Refer to the reviews and usage experience of other users.
Choose devices with good reputation and high user satisfaction.
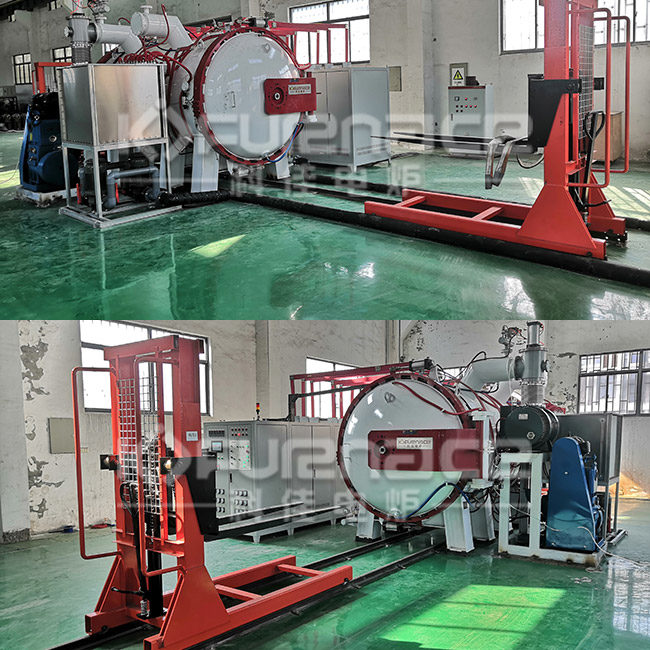
Industrial vacuum furnace (click on the image to view product details)
In general, when choosing a vacuum furnace for silicon carbide sintering, multiple aspects should be considered comprehensively to ensure that the selected equipment meets production needs, improves product quality and production efficiency. At the same time, it is recommended to compare and evaluate products from multiple manufacturers before actual purchase, and choose equipment that is more suitable for one’s own production needs.Click to learn more Vacuum Furnaces! Or click on online customer service to learn more about product information!