In the process of using PECVD (plasma enhanced chemical vapor deposition) coating electric furnace, in order to ensure the safe operation of the equipment and the quality of the coating, the following aspects need to be noted:
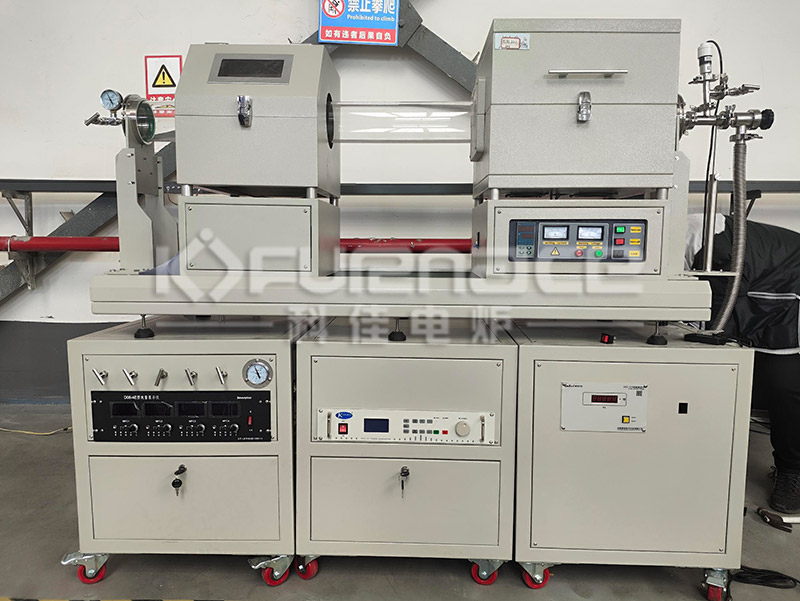
Slide PECVD tube furnace (click on the picture to view product details)
1. Equipment installation and preparation
Equipment installation:
Follow the equipment operation manual and install the equipment in the correct order.
Ensure that all components are tightly connected, such as electrode connections, quartz tube joint assembly, vacuum pump connections, etc.
Pay special attention to the position of sealing components such as rubber rings to avoid damage during the tightening process.
Equipment cleaning:
Before use, thoroughly clean the reaction chamber, pipelines, valves, and other components to ensure that there are no impurities.
Use disposable latex finger cots and other tools to avoid direct contact with seals or other sensitive parts with bare hands.
Gas preparation:
Check the supply of gases required for coating, such as SiH ₄, NH ∝, etc.
Ensure that the gas pipeline is connected correctly and firmly, and that the gas pressure meets the requirements.
Ensure that the gas purity meets the standards specified by the equipment.
2. Equipment startup and parameter settings
Device startup:
Follow the equipment operation manual and start the equipment in the correct order.
After startup, check and set various parameters through the touch panel, such as gas flow rate, tube furnace temperature curve, RF power, etc.
Parameter settings:
According to the coating process requirements, accurately set the gas flow rate.
Set the heating program for the tube furnace to ensure that the temperature curve meets the requirements.
To adjust the RF power, usually adjust the vacuum degree in the tube before starting the glow. The RF power setting should be reasonable to avoid too high or too low.
3. Coating process monitoring
Monitoring equipment parameters:
During the coating process, closely monitor the changes in parameters such as vacuum degree, gas flow rate, temperature, and RF power.
If there is any abnormality, the coating operation should be stopped immediately, the cause should be identified and dealt with.
Observe the coating condition:
Regularly check the coating effect, such as film thickness, uniformity, adhesion, etc.
If abnormal coating is found, adjust the process parameters or stop coating in a timely manner.
4. Equipment shutdown and subsequent processing
Device shutdown:
After the coating is completed, turn off the equipment in the order specified in the equipment operation manual.
First, turn off the RF generator, then turn off the tube furnace and vacuum pump, and finally turn off unrelated gases.
Subsequent processing:
After turning off the device, wait for it to cool down to a safe temperature and clean the remaining coating materials, dust, and other impurities inside the device.
Use specialized cleaning tools and cleaning agents for cleaning, but be careful to avoid corrosion of equipment components caused by cleaning agents.
5. Safety and Maintenance
Safety measures:
Strictly follow the operating procedures and safety rules during the operation process.
Equipped with a separate regulated power supply and grounding system to ensure stable power supply.
Regularly check the safety performance of the equipment, such as whether the cable contact is good, whether the vacuum pump is normal, etc.
Equipment maintenance:
Regularly maintain and upkeep the equipment, including replacing vacuum pump oil, checking seals, cleaning target materials, calibrating instruments, etc.
The maintenance cycle depends on the frequency of use and working environment of the equipment. It is generally recommended to conduct an overall maintenance every certain period of time (such as 1-3 months) or after completing a certain coating task.
Establish equipment maintenance files to record information such as equipment operation, maintenance time, and content, in order to promptly identify potential issues with the equipment.
6. Other precautions
Sample processing:
When handling samples, avoid contaminating or damaging them.
Use specialized tools (such as quartz suction pens) for sample retrieval, placement, and transportation.
Process optimization:
Optimize the process and adjust parameters based on specific materials, pore structures, and requirements.
Through experiments and data analysis, continuously improve the quality of coating and production efficiency.
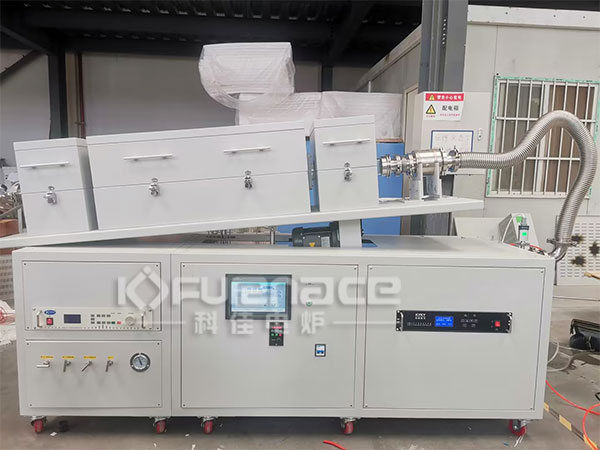
Customized tilted rotating PECVD coating electric furnace (click on the image to view product details)
In general, the use of PECVD coating electric furnace requires comprehensive consideration of equipment installation, parameter settings, coating process monitoring, equipment shutdown and subsequent processing, safety and maintenance, and other aspects. By strictly adhering to operating procedures and safety rules, strengthening equipment maintenance and upkeep, the safe operation and coating quality of the equipment can be ensured.Click to learn more PECVD devices! Or click on online customer service to learn more about product information!