Atmosphere furnace is commonly used in the sintering field of granular powders and other materials. As a commonly used equipment in the heat treatment industry, when choosing a 1400 ℃ atmosphere furnace, the following aspects should be noted:
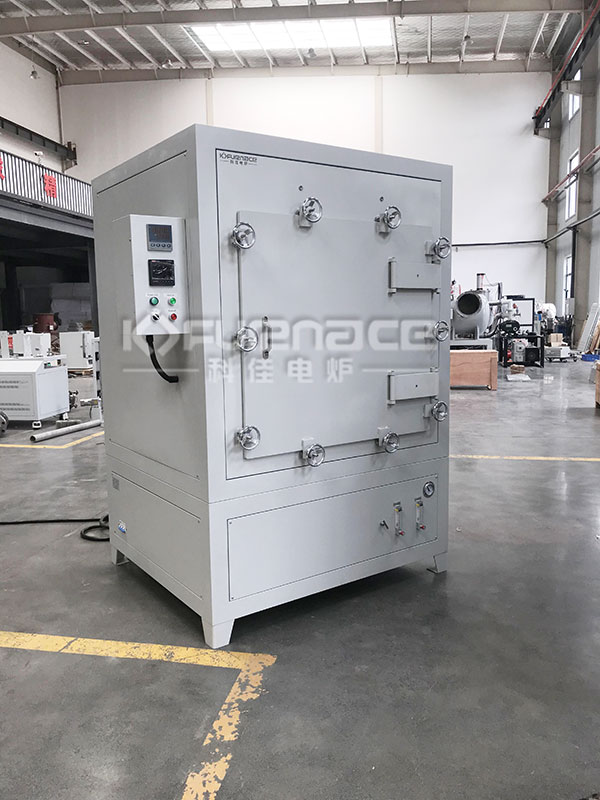
A commonly used atmosphere sintering furnace (click on the image to view product details)
1. Furnace structure and materials
Double layer furnace shell and air cooling system: It is preferred to choose an atmosphere furnace with a double layer furnace shell structure and an air cooling system in the middle. This design can effectively reduce the surface temperature of the furnace shell and achieve rapid temperature rise and fall.
Heating element: The heating element is the core component of the atmosphere furnace, and silicon carbon rods are often selected as high-temperature heating elements for 1400 ℃ due to their high heating efficiency and good temperature uniformity.
Furnace material: The furnace material made of high-quality alumina polycrystalline fiber vacuum adsorption has good insulation performance, which can effectively reduce heat loss and make the temperature inside the furnace more uniform.
2. Sealing and vacuum performance
Sealing structure: The sealing performance of the furnace door, roof and other parts is very important. High temperature silicone rubber sealing and equipped with a water cooling system is a good choice to ensure sealing in high temperature environments and prevent gas leakage.
Vacuum requirement: Select an atmosphere furnace that can achieve the required vacuum degree based on specific material and process requirements. Generally speaking, for high-temperature furnaces, the vacuum degree may need to reach 1000Pa or even higher to effectively eliminate gases and impurities inside the furnace, reduce the possibility of oxidation and pollution.
Extraction rate: The extraction rate of the vacuum system should be fast enough to quickly extract the gas inside the furnace before heating, achieve the required vacuum degree, and compensate for the decrease in vacuum degree caused by material deflation and other factors in a timely manner during operation.
3. Atmosphere control and gas flow rate
Atmosphere type: Select an atmosphere furnace that can be filled with various gases such as argon and nitrogen according to experimental or production needs to meet the requirements of different material processing processes for the atmosphere.
Gas flow control: Accurately control the gas flow rate through flow meters and pressure reducing valves to ensure the stability and uniformity of the atmosphere.
4. Intelligent temperature control system
Temperature control accuracy: Priority should be given to equipment with high temperature control accuracy. Equipment with temperature control accuracy of ± 1 ℃ or even higher is more suitable for experiments or processes that require high temperature control.
Heating rate: An atmosphere furnace that can reach the set temperature in a short period of time can save experimental time and improve work efficiency.
Multi stage temperature rise and fall program: It has the ability to set multiple temperature rise and fall programs, which can meet the requirements of complex sintering processes.
5. Safety and Energy Efficiency
Safety protection device: The atmosphere furnace with multiple safety protection devices such as overtemperature alarm, overcurrent protection, and disconnection protection can automatically cut off the power supply in a timely manner when the equipment encounters abnormal situations, ensuring the safety of experimental personnel and the normal operation of the equipment.
Energy saving effect: An atmosphere furnace using efficient heating elements and good insulation materials can reduce energy consumption and extend the service life of equipment. At the same time, the atmosphere circulation device inside the furnace can ensure the uniform distribution of atmosphere, further improving the reliability of experimental results.
6. Other considerations
Furnace size: Select the appropriate furnace size based on the size and quantity of materials to be processed in experiments or production, to ensure that the materials can be uniformly heated inside the furnace while avoiding space waste.
Automation level: Consider the automation level of the equipment, such as whether it has functions such as automatic vacuum pumping, inflation, heating, cooling, and whether it can achieve remote monitoring and data recording analysis. Highly automated equipment can improve work efficiency and accuracy of experimental results.
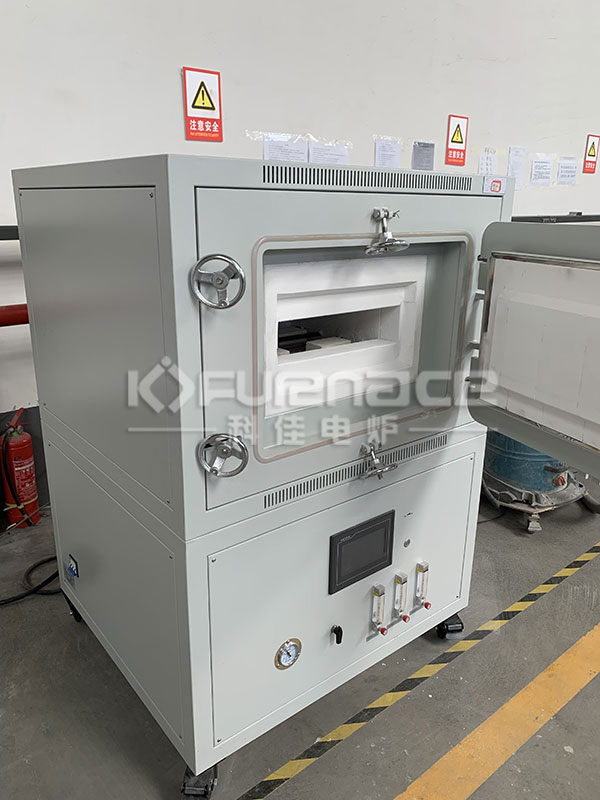
Customized furnace size and atmosphere furnace (click on the image to view product details)
In general, when choosing a 1400 ℃ atmosphere furnace, it is necessary to comprehensively consider multiple aspects such as furnace structure and materials, sealing and vacuum performance, atmosphere control and gas flow rate, intelligent temperature control system, safety and energy saving, as well as furnace size and automation level. By comprehensively evaluating these factors, one can choose an atmosphere furnace that is more suitable for their needs.Click to learn more Atmosphere Furnaces! Or click on online customer service to learn more about product information!