The use of PECVD (Plasma Enhanced Chemical Vapor Deposition) electric furnace coating for photovoltaic materials is a complex but precise process. Let’s take a look at the specific content of PECVD below!
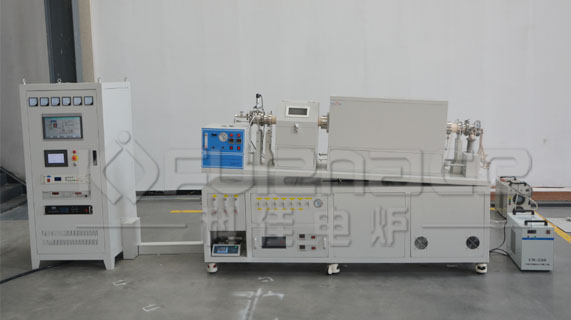
Commonly used tubular PECVD electric furnace (click on the image to view product details)
1. Introduction to PECVD Coating Technology
PECVD is a method of thin film deposition using plasma enhanced chemical vapor deposition technology. It uses low-temperature plasma to induce glow discharge at low pressure in the deposition chamber cathode. This discharge or other heating device can raise the temperature of the sample to a predetermined level, and then introduce a controlled amount of process gas. These gases undergo a series of chemical and plasma reactions, ultimately forming a solid thin film on the surface of the sample.
2. PECVD coating steps
Plasma excitation:
By applying external energy (such as radio frequency power or microwave power) to excite gas and generate plasma.
Gas molecules undergo ionization under the action of an electric field, producing charged ions and free electrons.
These charged particles accelerate under the action of an external electric field, forming plasma.
Introduction of sedimentary precursors:
Introduce precursor gases (such as silane, ammonia, etc.) for depositing thin films into the reaction chamber.
These gases undergo chemical reactions under the action of plasma, producing substances that deposit thin films.
Surface reaction:
Under the action of plasma, precursor gas molecules undergo ionization, excitation, dissociation and other reactions, generating active species (such as free radicals, ions, etc.).
These active species adsorb and undergo chemical reactions on the surface of the sample, forming a uniform and dense thin film.
Control sedimentation rate:
By controlling parameters such as gas flow rate, pressure, temperature, and plasma power in the reaction chamber, the deposition rate and film properties can be effectively controlled.
Film performance regulation:
By adjusting the process parameters of PECVD coating, such as deposition temperature, deposition time, gas ratio, etc., the properties of the film can be controlled.
For example, the refractive index, hardness, roughness, and other properties of the film can be adjusted to meet the needs of different applications.
3. Application of PECVD Coating in Photovoltaic Materials
PECVD coating technology has a wide range of applications in the field of photovoltaic materials, especially in the manufacturing of solar panels. Through PECVD technology, one or more thin films can be deposited on the surface of solar panels to improve their photoelectric conversion efficiency. These thin films typically include silicon nitride (SiNx) and other materials, which have excellent passivation and anti reflection properties, helping to reduce light loss and improve the conversion efficiency of the battery.
4. Precautions
Process stability: The PECVD coating process requires a high degree of process stability to ensure the uniformity and density of the film.
Safety performance: During operation, it is necessary to strictly comply with safety regulations to prevent dangerous situations such as gas leakage and electric shock.
Equipment maintenance: Regularly maintain and upkeep PECVD equipment to ensure its long-term stable operation and coating quality.
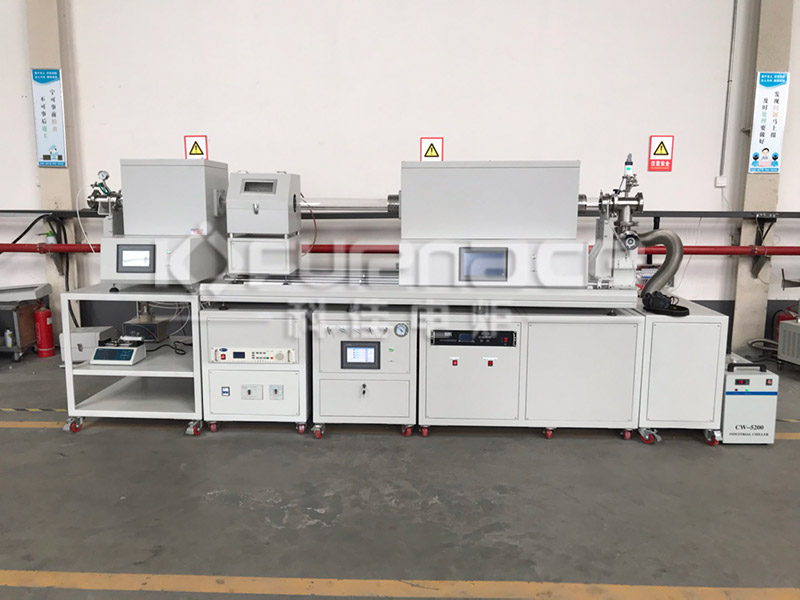
PECVD electric furnace with preheating (click on the image to view product details)
Overall, the use of PECVD electric furnace coating for photovoltaic materials is a precise and complex process that requires strict control of each step and parameter. By optimizing process parameters and film performance, it is possible to meet the needs of different application fields, especially in the manufacturing of solar panels, which plays a significant role.Click to learn more PECVD devices! Or click on online customer service to learn more about product information!