When choosing a vacuum CVD coating furnace, multiple factors need to be considered to ensure that the selected equipment can meet specific process requirements. Let’s take a look at what aspects to pay attention to when choosing a vacuum CVD coating electric furnace!
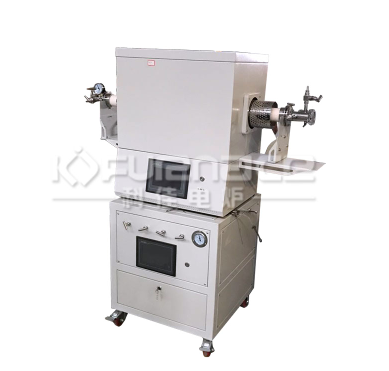
Commonly used CVD coating electric furnace (click on the image to view product details)
Application requirements:
Clarify the specific applications of CVD coating, such as growing thin films, synthesizing specific materials, etc. Different applications may require different types of CVD furnaces, such as low-pressure CVD, plasma enhanced chemical vapor deposition (PECVD), etc.
Material type:
Select a suitable CVD furnace based on the characteristics and properties of the required materials. For example, organic materials may require low-temperature CVD, while inorganic materials may require high-temperature CVD.
Working temperature range:
Determine the required operating temperature range for CVD process and select a furnace that can meet this requirement. Different furnaces have different maximum and minimum temperature limits.
Furnace tube material:
The material of the furnace tube has a significant impact on the CVD process. Common furnace tube materials include quartz, corundum, and metal. Quartz furnace tubes are suitable for high temperature and corrosive environments, while metal furnace tubes are suitable for environments that require higher vacuum levels.
Vacuum system:
For vacuum CVD coating furnaces, a vacuum environment is essential. Therefore, it is necessary to choose a suitable vacuum system, including the type of vacuum pump, pumping speed, and vacuum degree.
Furnace cavity size:
Select the appropriate furnace chamber size and volume based on the size and quantity of the processed samples. Ensure that the furnace chamber is large enough to accommodate the samples to be processed and maintain uniform deposition of the samples.
Heating method:
CVD furnaces can use different heating methods, such as resistance heating, induction heating, etc. Select the appropriate heating method based on the characteristics of the processed material and the requirements for heating uniformity.
Gas control system:
The CVD process requires precise control of gas flow rate and proportion. Therefore, it is necessary to choose a reliable gas control system, including the accuracy of gas flow meters, gas mixing methods, and gas supply methods.
Energy consumption:
Considering the energy consumption of CVD furnaces, choose equipment with high energy efficiency, energy conservation and environmental protection to reduce production costs and meet environmental requirements.
Security performance:
The furnace should have safety protection functions, such as overheating protection, gas leakage protection, etc., to ensure safety during operation.
Brand and Service:
Choose well-known and reputable manufacturers and brands to ensure product quality and reliable after-sales service. Before making a choice, you can consult professional technicians or manufacturers for evaluation and selection based on specific circumstances.
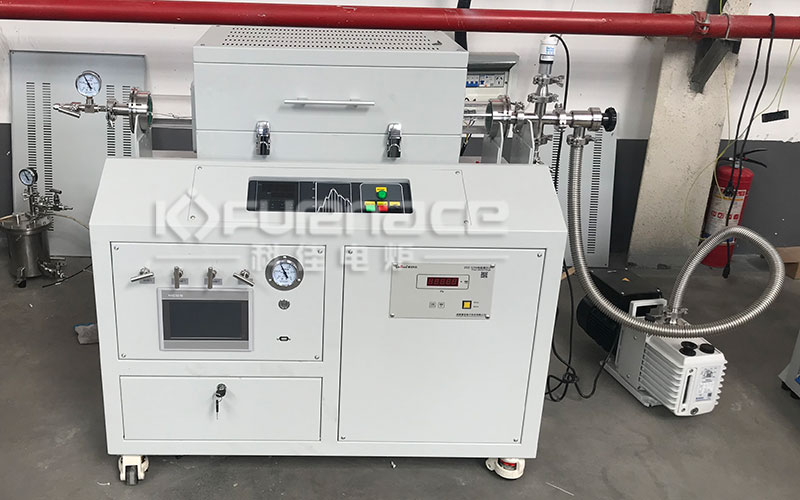
Touch screen CVD electric furnace (click on the image to view product details)
In general, when choosing a vacuum CVD coating electric furnace, multiple factors need to be considered, including application requirements, material type, operating temperature range, furnace tube material, vacuum system, furnace chamber size, heating method, gas control system, energy consumption, safety performance, and brand and service. By considering these factors comprehensively, it can be ensured that the selected equipment can meet specific process requirements and has good performance and reliability.Click to learn more CVD devices! Or click on online customer service to learn more about product information!