The rotary tube furnace has multiple advantages in the sintering process, mainly due to its unique rotary design and efficient heating performance. So what are the advantages of a rotary tube furnace during sintering?
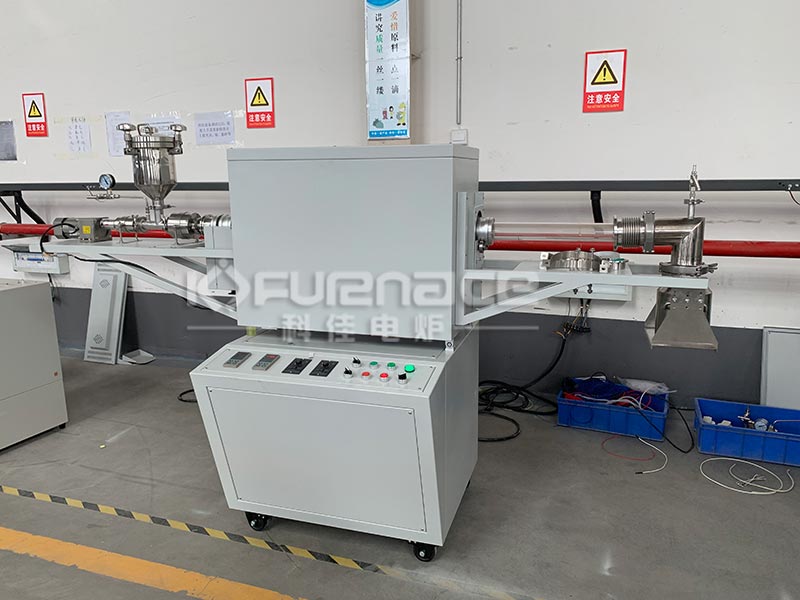
Commonly used high-temperature rotary tube furnace (click on the image to view product details)
1. Heating uniformity
Uniform heating: The rotating tube furnace is driven by an independent motor in the furnace to rotate the furnace tubes, allowing the heated materials to be fully mixed inside the furnace, thereby achieving uniform heating. This design reduces the temperature gradient and improves the heat treatment effect.
Temperature field balance: Adopting a double-layer shell structure and advanced temperature control system, such as a 30 stage or 40 stage programmed temperature control system, ensures the temperature balance inside the furnace, which is conducive to the uniform sintering of materials.
2. Wide applicability
Multi material processing: The rotary tube furnace is suitable for heating various materials, such as powders, particles, solids, etc., and can meet the sintering needs of different fields and materials.
Multi domain applications: Widely used in various fields such as ceramics, metallurgy, electronics, and new energy, especially in the preparation of high-performance materials, coatings, and films.
3. Temperature control accuracy
High precision temperature control: The rotary tube furnace can use a computer control system to achieve precise temperature control. The temperature controller is sensitive, capable of automatic constant temperature and time control, and has functions such as over temperature power-off alarm to ensure the stability and safety of the sintering process.
Multiple heating elements, such as silicon carbon rods, silicon molybdenum rods, or resistance wires, can be selected according to different needs to meet sintering requirements in different temperature ranges.
4. Efficient and energy-saving
Rapid temperature rise and fall: The furnace adopts high-efficiency insulation materials such as alumina ceramic fiber board, and the double-layer furnace shell is equipped with an air cooling system, which can quickly rise and fall the temperature and improve sintering efficiency.
Energy saving design: The energy-saving ceramic fiber material and double-layer structure design effectively reduce the surface temperature, minimize energy loss, and achieve energy-saving effects.
5. Easy operation and customizability
Easy to operate: Rotary tube furnaces typically have a simple and user-friendly interface and control system, allowing operators to easily master and perform sintering operations.
Customizability: The size of the furnace tube and the length of the heating zone can be customized according to customer requirements to meet the needs of different sintering processes. At the same time, optional accessories such as automatic feeding machines and angle measuring instruments can be equipped to improve the automation level of the sintering process.
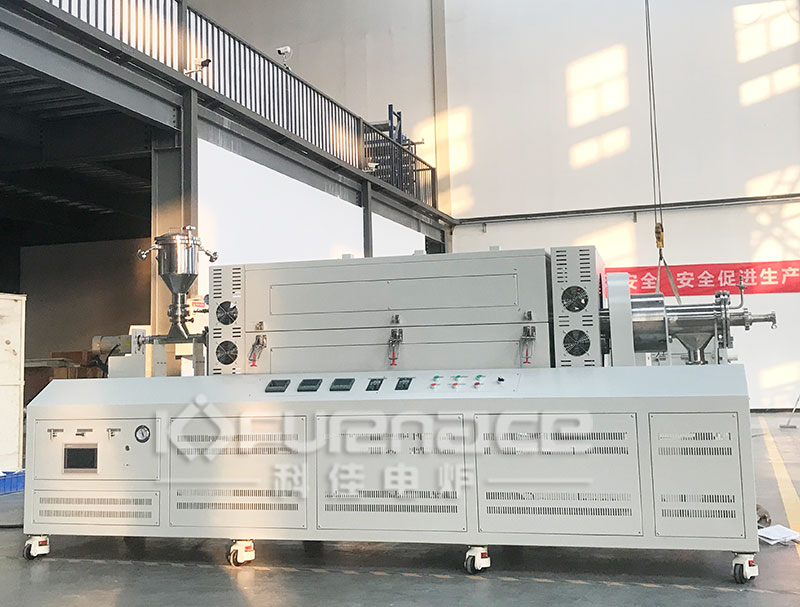
Multi temperature zone continuous feeding and discharging rotary tube furnace (click on the picture to view product details)
So, the rotary tube furnace has many advantages in the sintering process, such as uniform heating, wide applicability, accurate temperature control, high efficiency and energy saving, as well as easy operation and customization. These advantages have led to the widespread application and recognition of rotary tube furnaces in high-temperature heat treatment, sintering, and other processes in multiple fields.Click to learn more tube furnaces! Or click on online customer service to learn more about product information!