The principle of hot pressing sintering is to densify the powder material at high temperature and high pressure, thereby forming a dense solid material. This process combines the advantages of traditional sintering and pressure processing, which can greatly improve the density and mechanical properties of the material.
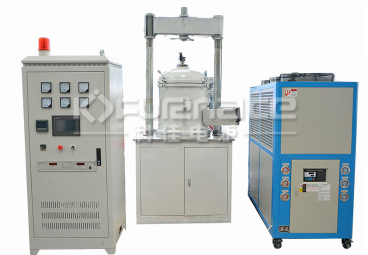
A commonly used vacuum hot pressing furnace (click on the image to view product details)
1. Basic process:
Add powder, usually metal, ceramic, or composite material powder, to the specified model and simultaneously heat and apply pressure from one axis.
Through this synchronous heating and pressurization method, plastic flow and contact occur between powder particles, ultimately increasing the density of the material and forming a hard sintered body.
2. Specific mechanism:
Surface diffusion: At high temperatures, diffusion occurs on the surface of powder particles, and as the contact area between particles increases, it facilitates the bonding between particles.
Plastic deformation: When powder particles are subjected to high pressure, plastic deformation occurs, causing more contact points between particles, thereby enhancing the bonding force between particles.
Material migration: Under the action of external pressure, the migration of materials is completed, and the densification of the sintered body mainly relies on the action of external pressure.
3. Heating:
Place the mold containing powder into the hot pressing equipment and heat it in a protective atmosphere (such as nitrogen, argon) or vacuum environment.
The heating temperature is usually below the melting point of powder materials, but sufficiently high to promote diffusion and sintering processes.
4. Apply pressure:
Apply high pressure (usually between tens to hundreds of megapascals) while heating.
Pressure directly acts on the powder through the mold, causing it to undergo plastic deformation and flow at high temperatures, filling the gaps between particles.
5. Sintering process:
The combined effect of heating and pressure causes diffusion and rearrangement of powder particles, increasing the contact area between particles and reducing internal pores.
The diffusion mechanism includes surface diffusion, grain boundary diffusion, and bulk diffusion, which form a strong bond between particles.
6. Cooling and demolding:
After maintaining pressure and temperature for a period of time, gradually cool the mold and sample while maintaining pressure to prevent sample shrinkage and deformation.
After cooling to room temperature, release the pressure and remove the densified sintered body from the mold.
7. Characteristics of hot press sintering:
Low molding pressure: Due to the simultaneous heating and pressurization, the powder is in a thermoplastic state, which facilitates the contact diffusion and flow mass transfer of particles. Therefore, the molding pressure is only 1/10 of that of cold pressing.
Lowering sintering temperature: Compared to atmospheric sintering, hot pressing sintering has a lower sintering temperature. For example, the sintering temperature of alumina under normal pressure needs to reach 1800 ℃, while under hot pressure (20MPa), it only needs to be sintered to around 1500 ℃, effectively saving energy and time.
Improving product performance: Hot pressing sintering can obtain products with small grains, high density, and good mechanical and electrical properties. The densified and homogenized microstructure enhances the strength, hardness, and toughness of the material.
Widely applicable: can be used for various materials, including metals, ceramics, composite materials, and difficult to sinter ultra-high temperature materials.
8. Application areas of hot press sintering:
Aerospace: Manufacturing high-performance, high-temperature resistant structural materials and turbine components.
Automotive industry: producing high-strength and wear-resistant engine components and transmission components.
Electronics and Semiconductors: Produce high-purity, high-performance electronic packaging materials and semiconductor components.
Medical devices: manufacture biocompatible implants and surgical tools.
Tools and molds: produce cutting tools and forming molds with high hardness and wear resistance.
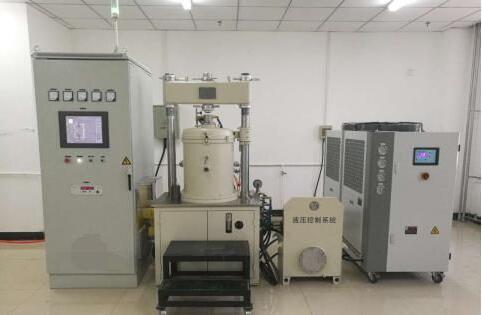
Graphite vacuum hot pressing furnace (click on the image to view product details)
Hot press sintering densifies powder materials under high temperature and high pressure to form high-density and high-performance solid materials. This process has important applications in the fields of materials science and engineering, and is an effective method for manufacturing high-quality, complex shaped materials.Click to learn more heat treatment furnace! Or click on online customer service to learn more about product information!