When selecting a CVD (Chemical Vapor Deposition) furnace, multiple factors need to be considered to ensure that it meets specific process requirements. Here are some key selection steps and considerations:
Determine process requirements:
Sedimentary materials: Clearly define the types of materials that need to be deposited, such as metals, ceramics, semiconductors, etc.
Sedimentation temperature: Understand the required deposition temperature range in order to select a CVD furnace that can withstand the corresponding temperature.
Sedimentation atmosphere: Determine the required atmosphere during the deposition process, such as nitrogen, argon, hydrogen, etc., as well as the purity requirements of the atmosphere.
Deposition rate and uniformity: Determine the required deposition rate and film uniformity according to process requirements.
Furnace type selection:
Horizontal CVD furnace: suitable for deposition processes with large areas and high uniformity requirements.
Vertical CVD furnace: suitable for small area and high-precision deposition processes.
Other special furnace types: Select suitable furnace types according to specific process requirements, such as rotary, multi-source, etc.
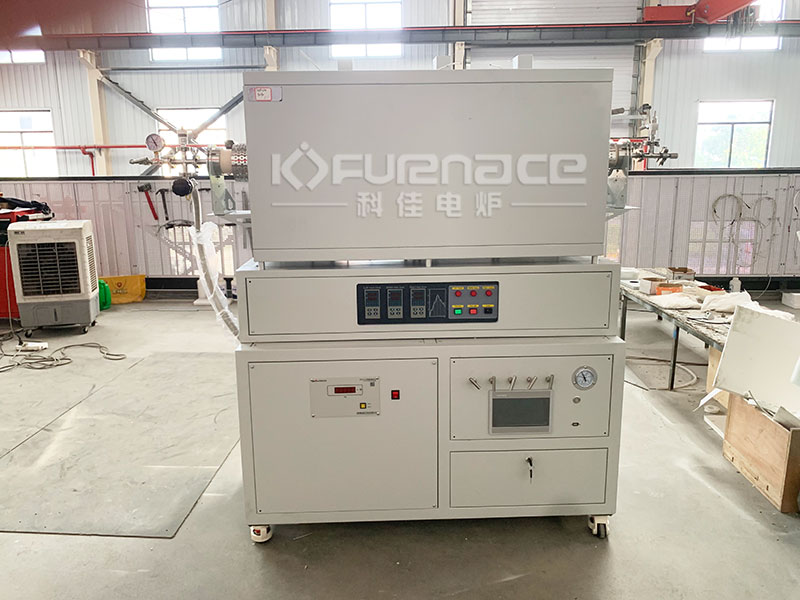
Multi temperature zone CVD furnace (click on image to view product details)
Heating method and temperature control:
Heating methods: Common heating methods include resistance heating, radiation heating, microwave heating, etc. Choose a suitable heating method to ensure temperature uniformity and stability inside the furnace.
Temperature control: Choose a high-precision and stable temperature control system to ensure precise temperature control during the deposition process.
Vacuum system:
Vacuum degree: Select the appropriate vacuum degree according to the process requirements to ensure that the deposition process is not affected by impurities.
Vacuum pump: Select a vacuum pump that is suitable for the process requirements, such as mechanical pump, molecular pump, etc.
Gas supply system:
Gas type and purity: Select the appropriate gas type and purity according to the process requirements.
Gas flow meter: Choose a high-precision and stable gas flow meter to ensure precise control of gas flow rate.
Furnace material and structure:
Furnace material: Choose materials that are resistant to high temperature, corrosion, and good thermal conductivity, such as quartz, stainless steel, corundum, etc.
Furnace structure: Ensure a compact and well sealed furnace structure to reduce heat loss and impurity entry.
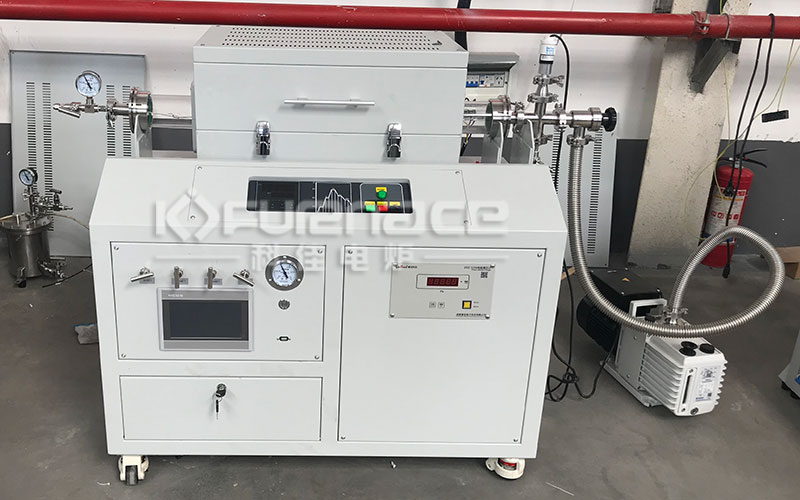
Commonly used CVD furnaces (click on the image to view product details)
Control system and automation level:
Control system: Choose a control system that is easy to operate and has complete functions to meet different process requirements.
Automation level: Select an appropriate level of automation based on actual needs to improve production efficiency and reduce labor costs.
Cost and budget:
Evaluate the price and performance of different models of CVD furnaces, and choose products with high cost-effectiveness.
Select the appropriate CVD furnace according to the budget to ensure a return on investment.
Manufacturer and brand:
Choose manufacturers and brands with rich experience and good reputation to ensure the quality of equipment and after-sales service.
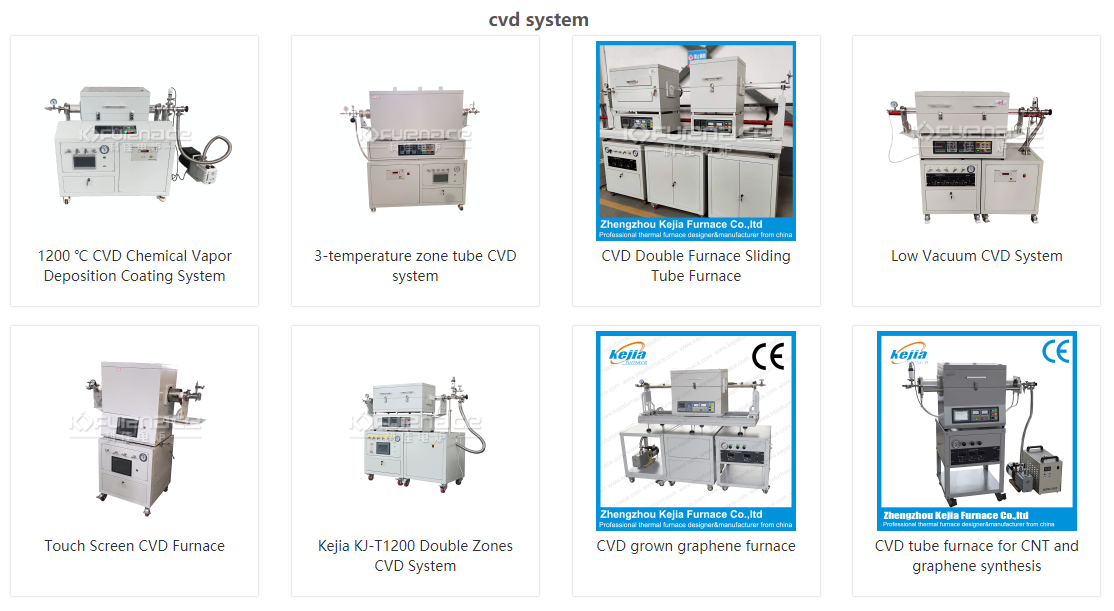
Various models of CVD furnaces (click on the image to view more CVD furnaces)
So choosing a suitable CVD furnace requires comprehensive consideration of multiple factors. It is recommended to have in-depth communication with manufacturers or professionals during the actual selection process to ensure that the selected equipment can meet specific process requirements.Click to learn more CVD devices! Or click on online customer service to learn more about product information!