The muffle furnace originated in 16th century Germany, but was mainly used for making glass at that time. In the early 19th century, British inventor Henry John Maw improved this glass making furnace by adding temperature control devices, making it suitable for producing higher quality glass and promoting its application on this basis. Therefore, this high-temperature treatment equipment is named the “muffle furnace”.
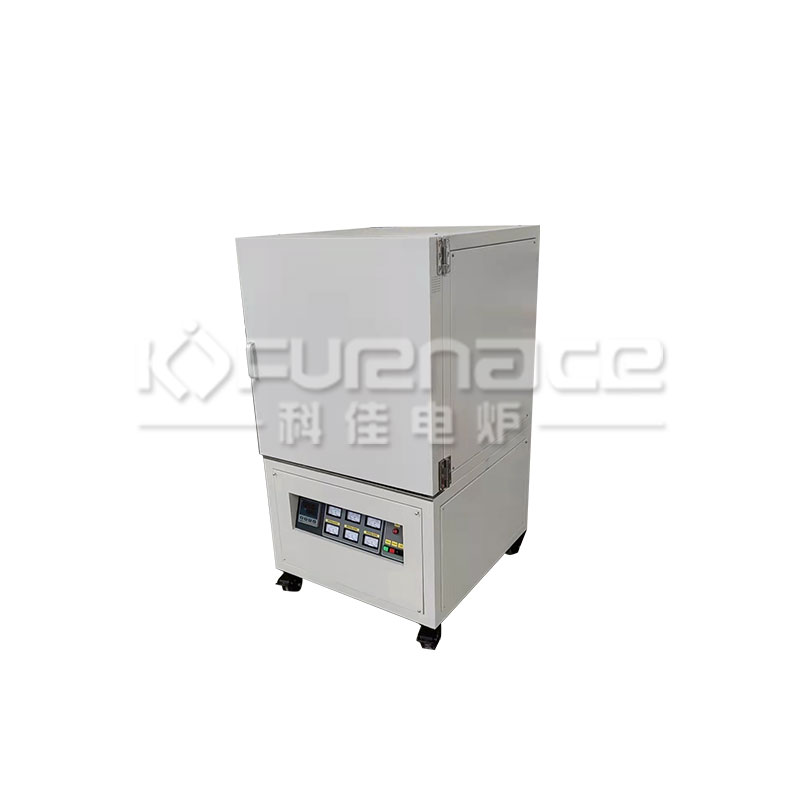
KJ-M1200-64L Muffle Furnace
Modern improved muffle furnace, also known as box furnace, is a universal heating equipment. It is box type, with resistance wires hidden in the box. The furnace wall is thick, with insulation materials inside, and the temperature can rise to 1200 degrees. It is commonly used in the muffle furnace for alkali melting of certain Refractory metals and minerals, as well as in gravimetric analysis, to ash filter paper without flame, burn and decompose organic matter, drive away volatile components in inorganic matter, etc. Its operation is simple, maintenance is convenient, and the furnace is equipped with a controllable chimney. Suitable for chemical analysis of coal, coking products, and chemical raw materials. It can be used in industries and departments such as electricity, coal, papermaking, petrochemicals, cement, agriculture and animal husbandry, pharmaceutical research, teaching, etc. A muffle furnace is a heating furnace with a box shaped furnace. During the entire heating process of heating, insulation, and cooling the product, the product remains stationary, and the feeding and discharging are carried out through a single door or slot. Also known as intermittent production furnace.
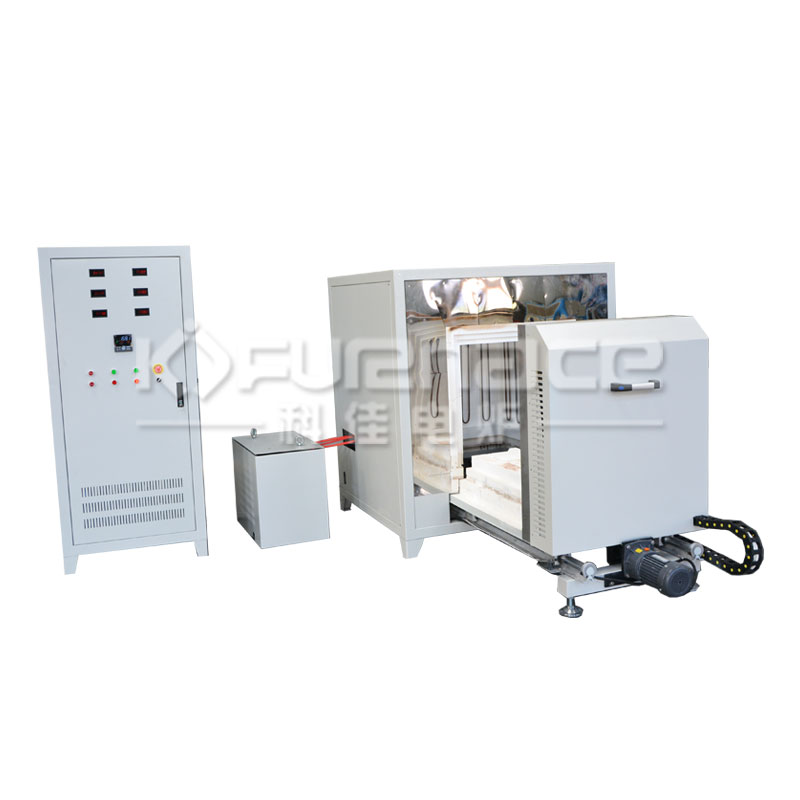
KJ-M1700-T216L Electric trolley furnace
The control system is integrated on the furnace body. Select an intelligent program temperature controller, and adjust the temperature curve through automatic control settings. The control variable is composed of linear combinations to control the controlled object. The temperature controller receives signals detected by thermocouples and controls the power module.
To prevent hot gas leakage in the furnace, a total of two layers of sealing are designed from the inside to the outside at the furnace door. The inner layer adopts a ceramic fiber rope sealing structure, and the outer layer is sealed with a silicone rubber sealing ring. To extend its service life, a stainless steel cooling water jacket is designed at the sealing point of the furnace mouth for cooling and cooling. The door lock adopts a multi-point handwheel rotation locking mechanism, which can evenly lock all around the door at the same time. In addition, the furnace door fixing device is installed on the end face of the furnace, using a movable double hinge mechanism that can move with the free extension of the furnace, providing better sealing effect. The furnace door can be designed to open downwards, upwards, at the top, and on both sides as needed.
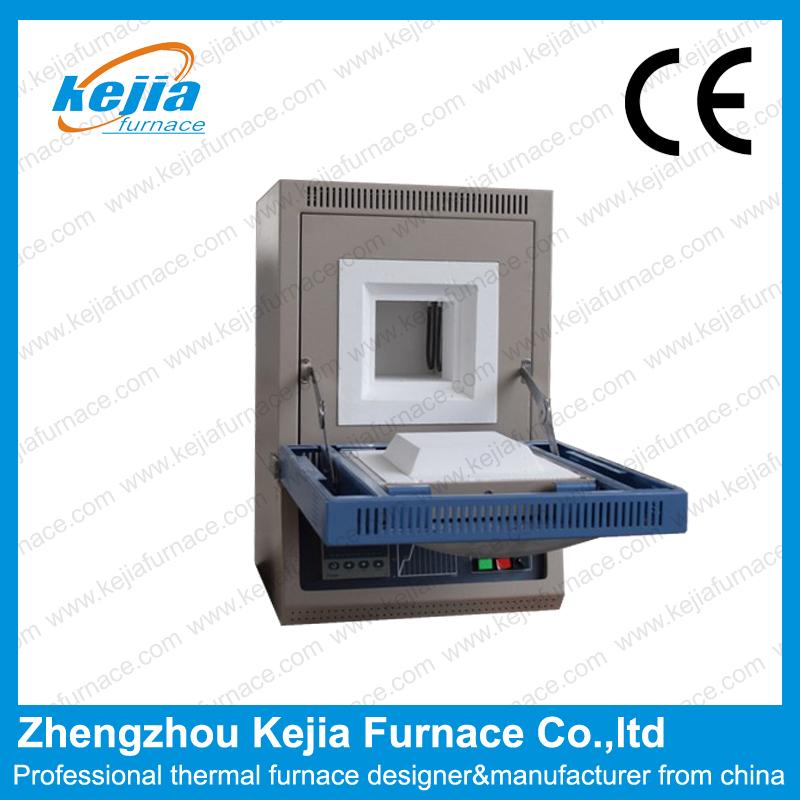
1700℃ Drop Down Door muffle furnace
The top of the equipment can be designed with exhaust chimneys as needed to discharge a large amount of exhaust gas and smoke generated during the heating process.
The temperature control system adopts an intelligent PID method to adjust the temperature, and can set a 30 segment temperature rise and fall program. The maximum temperature of the furnace is 1700 ℃. This furnace has the advantages of balanced temperature field, low surface temperature, fast temperature rise and fall rate, and energy conservation. It is an ideal product for high temperature sintering, metal annealing, and quality testing in universities, research institutes, and industrial and mining enterprises.
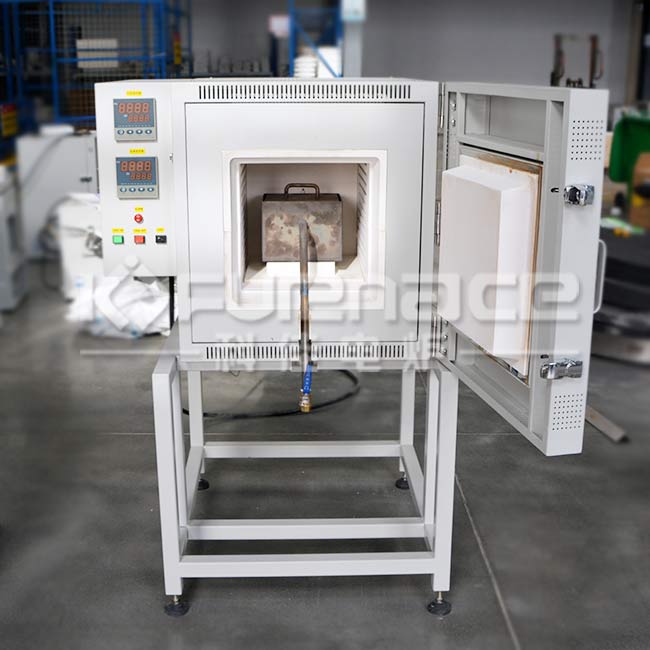
Box type pyrolysis carbonization furnace
Advantages of muffle furnace:
(1) Simple structure, excellent technology, durable product, easy and safe operation.
(2) Low operating and maintenance costs, long service life.
(3) Adopting humanized design, beautiful and elegant, easy to operate, the outer paint layer uses spray molding high-temperature baking process. It has the ability to withstand high temperature, oxidation, acid and alkali, and has better corrosion and oxidation resistance compared to the painting process. Choose a color tone that is resistant to aging and will not cause appearance color fading due to prolonged use.
(4) The furnace body adopts a stepped assembly structure, and the furnace door and furnace door frame adopt an overall design, effectively ensuring that the furnace top does not collapse. The close cooperation between the furnace door and the furnace door frame ensures that heat energy is not easily lost and increases the service life of the furnace door part. The furnace is equipped with a furnace frame, which can achieve layered management and placement of materials according to user production needs, and the materials can be fully burned.