Vacuum furnace nitriding technology description
Time:2020-09-18 09:47 Click:
Nitriding is the use of a vacuum furnace to heat the steel parts as a whole, and a small amount of gas is filled to produce active nitrogen atoms in a low-pressure state to infiltrate and diffuse into the steel to achieve hardening; while ion nitriding is an active N produced by glow discharge Ion bombardment only heats the surface of the steel parts, and a chemical reaction occurs to produce nuclei to achieve hardening. By infiltrating nitrogen into the box furnace and the atmosphere furnace, the hardening density is achieved and the texture is harder.
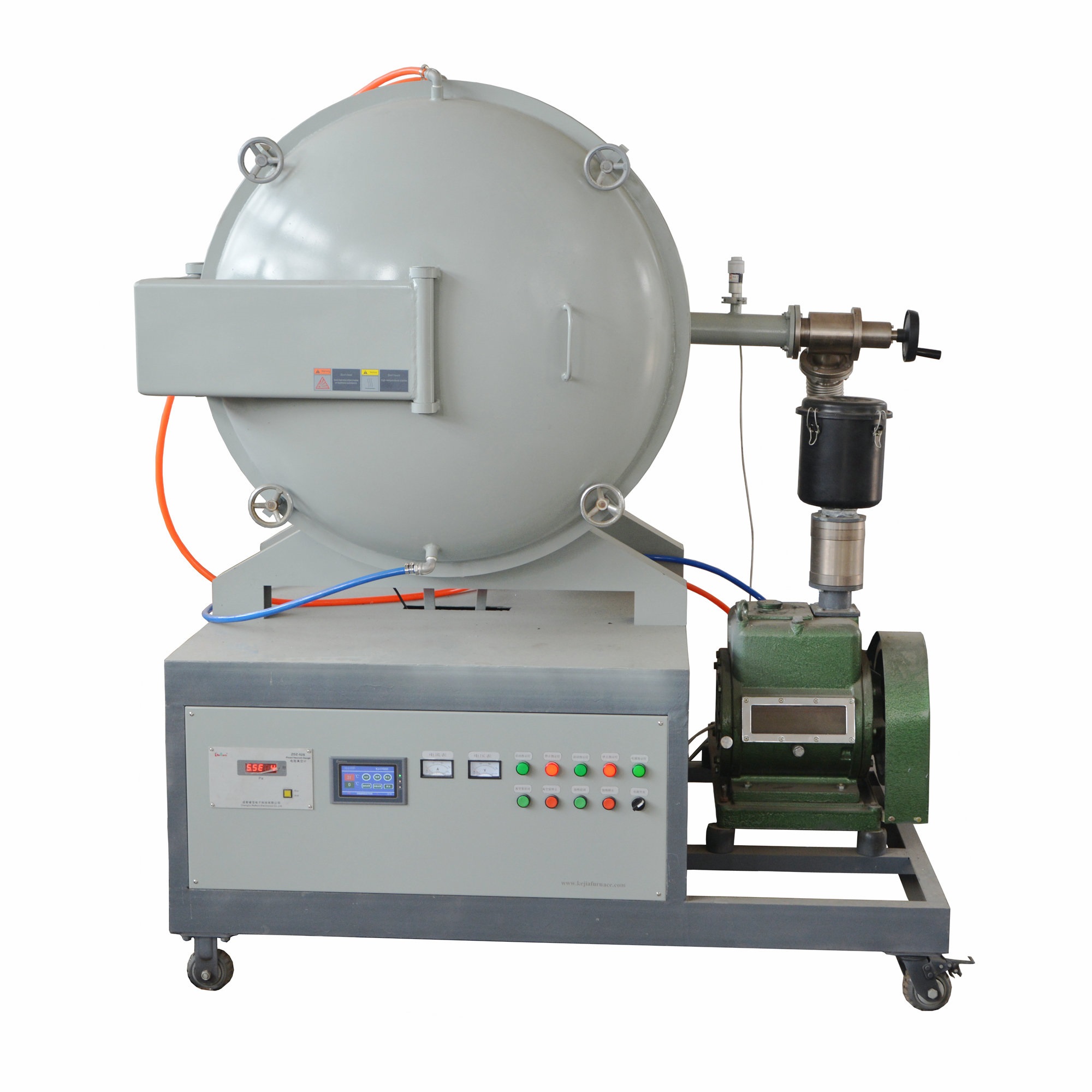
When infiltrating the atmosphere, the vacuum furnace is exhausted to a higher vacuum of 0.133Pa (1×10-3 Torr), and the workpiece is raised to 530~560℃. At the same time, it is fed with ammonia gas mainly containing active substances. A composite gas, and precise control of the feeding amount of various gases, the vacuum furnace pressure is controlled at 0.667Pa (5Torr), after holding for 3 to 5 hours, the inert gas in the furnace is used for rapid cooling. Different materials, after this treatment, a hardened layer with a penetration depth of 20-80μm and a hardness of 600-1500HV can be obtained.
Vacuum nitriding is called vacuum exhaust nitrocarburizing. Its characteristic is to activate and purify the metal surface through vacuum technology. In the entire heat treatment process of heating, heat preservation and cooling, the impure trace gas is discharged, and the pure composite gas containing the active material is sent in, making it possible to adjust and control the surface layer phase structure, improve quality, and increase efficiency. . X-ray diffraction analysis confirms that after vacuum nitriding, the compound layer in the nitriding layer is ε single-phase structure without other brittle phases (such as Fe3C, Fe3O4), so the hardness is high, the toughness is good, and the distribution is good.
The achievable hardness of the "white layer" single-phase epsilon compound layer is related to the material composition. The higher the Cr content in the material, the higher the hardness. When Cr is 13%, the hardness can reach 1200HV; when Cr is 18% (mass fraction, the same), the hardness can reach 1500HV; when Cr is 25%, the hardness can reach 1700HV.
The wear resistance of the single-phase epsilon compound layer without brittle phase is higher than that of the gas nitrocarburizing structure, and it has excellent resistance to friction and burn, resistance to heat bonding, resistance to welding, and resistance to melt loss. However, the existence of this "white layer" also has disadvantages for some molds and parts. It is easy to cause cracks in the forging die at the early stage of forging, and pinholes are easily generated during welding repair.
Another advantage of vacuum nitriding is that by controlling the type and amount of the composite gas containing activated substances fed into the furnace, it is possible to obtain a structure with almost no compound layer (white layer) but only a diffusion layer. The reason may be formed after the vacuum furnace is exhausted to 0.133Pa (1×10-3 Torr). Another reason is the structure formed by the diffusion of the composite gas with the active material into the steel in a short time. The advantages of this structure are excellent thermal shock resistance and crack resistance. Therefore, for hot work molds that are subjected to high temperature tempering, such as high-speed steel or 4Cr4MoSiV (H13) steel molds, the comprehensive properties of high surface hardness, good wear resistance, good thermal shock resistance, crack resistance and toughness can be obtained. ; But when there is only the diffusion layer structure, the seizure resistance, welding resistance and melt loss performance of the mold is not good enough.
Due to the different service conditions and performance requirements of molds or mechanical parts, it is necessary to adjust the structure and performance of the surface layer during surface heat treatment. In addition to the application of vacuum nitriding to molds, it has obvious effects on improving the performance of precision gears, mechanical parts that require wear and corrosion resistance, and springs. The materials that can be processed are also relatively wide.
Please leave a message here. We will reply you in 24 hours.